Project Overview:
Dhanvi Infracon Pvt. Ltd. partnered with Emnis System Pvt. Ltd., a leading manufacturer of Electrical Panels, Automation Systems, and Enclosure Solutions, to construct a state-of-the-art manufacturing and R&D facility. The facility was designed to reflect the technological advancement and precision engineering core to Emnis’s operations. The comprehensive construction included production floors, testing labs, assembly zones, secure storage, R&D spaces, and modern office spaces—optimized for high-voltage equipment handling and safety.
Key Features of the Project:
- Built-up Area: Over 85,000 sq. ft. of constructed space
- Structural Design: RCC and pre-engineered building (PEB) hybrid structure
- Utilities: Embedded high-capacity electrical ducting and dedicated HVAC
- Functional Zones: Assembly bays, testing labs, panel production areas, and administrative blocks
- Green Building Design: Low-energy lighting, water recycling systems, and efficient insulation
- Fire & Safety Compliance: Complete fire suppression system, emergency exits, and surveillance
- Automation Ready: Smart-enabled power grids and IoT-compatible infrastructure
- Parking & Movement: Ample industrial vehicle circulation space and loading/unloading zones
Construction Technologies Used:
- Pre-Engineered Buildings (PEB):
Enabled quicker timelines, reduced costs, and ensured design flexibility for panel height requirements. - Smart Building Integration:
IoT-compatible wiring systems and automation support ensured Emnis could integrate SCADA and PLCs across its facility. - Low-Voltage Cabling Infrastructure:
Specialized cable trays, raceways, and trenching for safe handling of low-voltage electrical circuits. - High Load-Bearing Flooring:
Industrial-grade epoxy flooring laid over RCC slabs to handle heavy machinery and reduce wear and tear. - Energy-Efficient Ventilation and Air Management Systems:
Ventilation design for heat-sensitive electronic assembly and high-precision labs. - BIM (Building Information Modeling):
Used for structural conflict detection, MEP alignment, and accurate site execution planning.

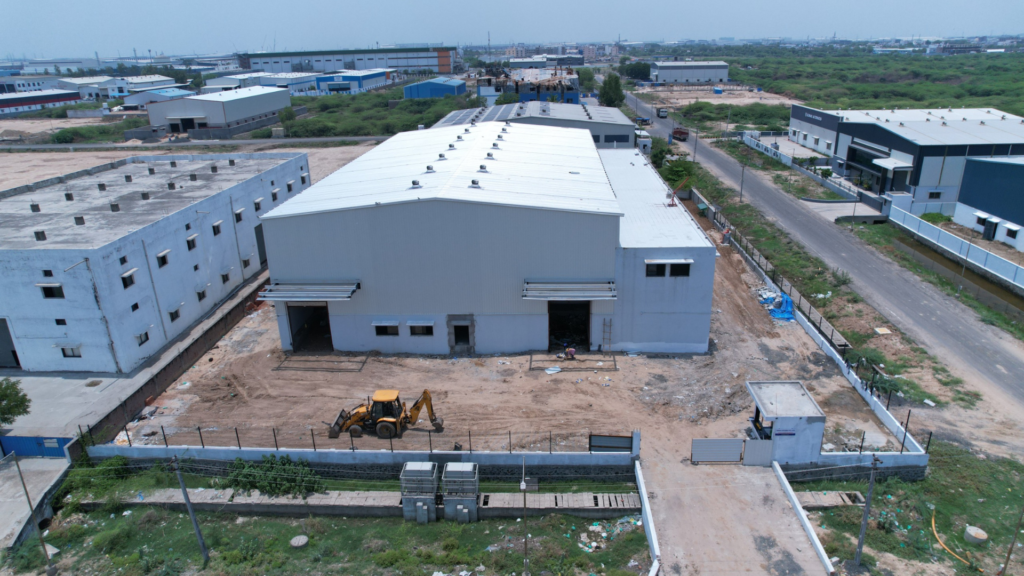
Challenges Faced During Construction:
- Precision Requirements:
Electrical panel manufacturing requires dust-free, temperature-controlled areas. Dhanvi’s team had to adapt civil construction to technical tolerances typical of cleanroom-like environments. - Underground Cabling & Safety:
Extensive sub-surface conduit layout needed risk-managed excavation and structural planning. - Real-time Adaptation:
As Emnis’s automation scope grew, Dhanvi Infracon modified the cable trenching design and electrical routing in real time, requiring coordination with multiple sub-vendors. - Timeline Pressure:
With market demand increasing, the project timeline was aggressive. Night shifts and phased construction helped meet deadlines. - Power Infrastructure:
Installation of dual transformer rooms and generator foundations for uninterrupted operations posed logistical and structural integration challenges.
Future Plans of the Facility:
- Automation Research Centre Expansion:
Emnis plans to add a research wing dedicated to AI-based automation technologies in the next phase. - Solar Integration:
Dhanvi Infracon has reserved rooftop and facade space for a 150 kW solar PV system planned for Phase 2. - Export-Oriented Assembly Lines:
The client is planning to introduce dedicated export lines with robotic support, which would require future MEP expansion. - Smart Factory Upgrade:
The client aims to implement a smart factory with real-time production monitoring, AI analytics, and predictive maintenance systems.
Advantages of the Project:
- Precision Infrastructure Tailored to Electrical Engineering
- High Energy Efficiency Reducing Operational Costs
- Future-Ready Design Allowing Seamless Expansion
- Low Maintenance Finishes Ensuring Long-Term Durability
- Enhanced Safety with Modern Fire and Monitoring Systems
Disadvantages & Mitigations:
Disadvantage | Mitigation |
---|---|
High initial investment in smart-ready infrastructure | Cost recovered via long-term savings in energy and maintenance |
Tight construction timeline | Multi-phase execution and 24/7 work schedule implemented |
Space constraints in the urban industrial area | Optimized multi-story design for storage and control rooms |
Risk of underground cabling damage | Used ground-penetrating radar (GPR) and experienced trenching experts |
Construction Management Insights:
- Real-Time Progress Tracking using integrated digital project dashboards.
- Collaborative Decision-Making with Emnis’s engineering team for real-time issue resolution.
- Strict Quality Control Audits at each milestone including MEP, civil, and finishing phases.
- Safety Protocols maintained throughout including PPE, scaffolding checks, and weekly toolbox talks.
- Third-party Inspection ensured compliance with BIS, IS, and NFPA standards.
Conclusion:
Dhanvi Infracon Pvt. Ltd. successfully delivered a technically advanced manufacturing unit for Emnis System Pvt. Ltd., aligned with the modern demands of electrical and automation production. The integration of smart technologies, thoughtful planning, and engineering finesse allowed Emnis to transition smoothly into a high-capacity, export-ready operation. This project stands as a benchmark in advanced industrial construction and is a testament to Dhanvi’s commitment to quality, adaptability, and futuristic design.